BeginnersSet upEffects
Gibson ROBOT Les Paul Studio Electric Guitar Metallic Green
(2)|Q&A|Item #:1273888007744 POS #:104921085
6-month special financing^ + $139 back in Rewards** Limited time Learn More
Lease-To-Own Purchase OptionsLearn more
Need Help?
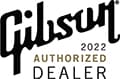
Description
The revolutionary Gibson Robot Les Paul Studio Limited Electric Guitar has some groundbreaking controls at its heart. At first glance, the four control knobs seem to be indistinguishable from those on other Les Paul guitars. But look again. While the four knobs do provide the standard tone and volume controls for each of the two pickups, the Multi-Control Knob (MCK) ” the one with the illuminated top ” serves as the master control for all aspects of the Robot Les Paul Studio Limited's amazing self-tuning system.
The MCK is what is commonly referred to as a "push-pull" knob. When down in the normal position it behaves as a regular volume or tone pot. When the MCK is pulled out, the Robot Les Paul Studio Limited's radical self-tuning system is activated and ready for use. It immediately places the Robot Les Paul Studio Limited in standard tuning mode (A440). A quick turn of the MCK presents 6 factory presets, all of which can be customized. At any time, you can also restore the tunings to the factory presets and start all over again. The LED display on top of the MCK also lets you know when a string is out of tune, or when all strings are in tune, and even when the tuners are turning to get them in tune. It also guides the setting of accurate intonation. At the end of the tuning process, the blue lights on top of the MCK flash. Push the MCK back in and it's ready to go. Now the only thing you have to do is play.
Featuring a performance-safeguarding Neutrik jack, which secures the cord into the guitar, the Robot Les Paul Studio offers all the power, tone, and performance of a traditional Studio model, with the revolutionary Robot automatic tuning.
Neutrik jack
Neutrik has been making superior electronic interconnection products since 1975, making them the logical choice to supply the performance-safeguarding jack in Gibson's revolutionary Robot Les Paul Studio Limited. Like many Neutrik products, the jack in the Robot Les Paul Studio Limited is manufactured from strong, high-grade thermoplastics and housed in a rugged die-cast nickel shell. A retention spring inside the jack ensures optimum grip on any guitar cable, thus avoiding the chance of lost connection.
ChamberingChambering
There's something about playing a Gibson Les Paul with perfect tone, balance, and weight. One of the ways the expert craftsmen at Gibson USA achieve this equilibrium is by carving carefully mapped-out chambers in the solid mahogany backs of Les Pauls using a Computer Numeric Controlled (CNC) router before the maple top is glued on. The positioning of the routs was established after careful examination of the resonant characteristics of the Les Paul. Gibson approached this process with the awareness that every change to the formula would have repercussions on the instrument's sound. The results are comfortable, lightweight guitars that are acoustically louder, with increased sustain and resonance.
Mahogany Body and Maple Top
There isn't anything more fundamental to a Les Paul than a mahogany back with a maple top, as well as the process involved in selecting the right wood and the formula to dry it out. First, every piece of wood is personally inspected and qualified by Gibson's team of skilled wood experts before it enters the Gibson factories. Once inside the Gibson factories ” where humidity is maintained at 45 percent, and the temperature at 70 degrees ” all woods are dried to a level of "equilibrium" by ensuring the moisture content does not change during the manufacturing process. This guarantees tight fitting joints and no expansion, and helps control the shrinkage and warping of the woods, in addition to helping reduce the weight. It also helps with improving the wood's machinability and finished properties, and adherence to glue. Consistent moisture content means that a Gibson guitar will respond evenly to temperature and humidity changes long after it leaves the factory.
Nitrocellulose Finishes
Applying this nitro finish to any Gibson guitar ” including the Robot Les Paul Studio Limited ” is one of the most labor-intensive elements of the guitar-making process. A properly applied nitro finish requires extensive man hours, several evenly applied coats, and an exorbitant amount of drying time. But this fact has never swayed Gibson into changing this time-tested method that has been employed ever since the first Gibson guitar was swathed with lacquer back in 1894. Why? For starters, a nitro finish dries to a much thinner coat than a polyurethane finish, which means there is less interference with the natural vibration of the instrument, allowing for a purer tone. A nitro finish is also a softer finish, which makes it easily repairable. You can touch up a scratch or ding on a nitro finish, but you can't do the same on a poly finish. In addition, a nitro finish is very porous in nature, and actually gets thinner over time. It does not seal wood in an airtight shell ” as a poly finish does ” and allows the wood to breathe and age properly.
Tune-control Bridge and Data Transmitting Tailpiece
The revolutionary Robot Les Paul Studio Limited sports a unique, highly specialized Tune Control Bridge, which acts as one of the main components of the self-tuning robotic system. The Tune-Control Bridge is a modified Tune-o-matic that measures the individual tuning of each string via special saddles. The signal from each string is then transmitted to the control CPU in the control panel, which then transfers the signal to the Neck CPU and the Powerhead Locking Tuners, which, in turn, tune the strings. At first glance, the tailpiece on Gibson's groundbreaking Robot Les Paul Studio Limited looks like a normal tailpiece. But look a little closer and you'll see that it's far from ordinary. Gibson's Data Transmitting Tailpiece is a hub of activity. First, each string is separated by ceramic insulators that isolate each individual string signal and avoids confusion as to which string is being processed and tuned. There are also special isolating inserts that keep the ball ends commonly found on electric guitar strings from making contact and disrupting signal flow. Underneath the tailpiece is a tiny circuit board that processes each individual signal to the ribbon cable, which is then transmitted to the on-board CPUs. Both pieces work with each other to help balance all the information being transmitted between the various points, and makes sure every string is in tune.
The mid to late 1960s saw the emergence of a very different type of music coming from the clubs of England. The new genre's players were demanding more powerful amplifiers with increased volume outputs to satisfy their sonic explorations. This lead to a call for a more versatile pickup to split coils through a push/pull knob, and prevent the microphonic feedback that occurs when the volume is turned up to maximum levels. Gibson answered this call with the 490T and 490R pickups ("T" for treble, and "R" for rhythm), both with the traditional characteristics of the original "Patent Applied For" pickups, but with two key modifications. First, a four-conductor wiring scheme allows the 490s to be connected to any push/pull knob, which lets players split the coils and increase versatility. Gibson also introduced wax potting, which does away with any air space inside the pickup ” thus lessening the chances of microphonic feedback. The result is a humbucker with the tonal characteristics of an original PAF, with a slight increase in upper mid-range response. The Gibson 498T bridge pickup is the 490's ideal complement. Taking the 490 one step further, the 498 swaps the Alnico II magnet to an Alnico V, this making it slightly hotter with emphasis on mid-ranges and highs. The pole pieces on the 498T are also aligned a little further apart to accommodate the spacing of the strings at the bridge, which is different than the spacing of the strings at the neck. As with all Gibson pickups, every part is precisely manufactured at Gibson USA in Nashville, Tennessee.
Fret Wire
The fret wire on the revolutionary Robot SG Special Limited is a combination nickel and silver alloy (approximately 80 percent nickel and 20 percent silver) specifically designed for long life and superior wear. Gibson's traditional "medium-jumbo" fret wire is first shaped by hand, then cut to an exact 12" radius. After hand pressing it into the fingerboard, a machine press finished the job to eliminate the gap between the bottom of the fret wire and the fingerboard.
22-Fret Rosewood Fingerboard
Rosewood has always graced the fingerboards of the world's finest stringed instruments. The fingerboard on Gibson's Robot Les Paul Studio Limited is constructed from the highest grade Rosewood on the planet. It's personally inspected and qualified by Gibson's team of skilled wood experts before it enters the Gibson factories to be fitted onto the necks of the Robot Les Paul Studio Limited guitars. The resilience of this dense and durable wood makes the fingerboard extremely balanced and stable, and gives each chord and note clarity and bite. The 12" radius of the fingerboard provides smooth note-bending capabilities and eliminates "dead" or "choked out" notes, which can occur on fingerboards with lesser radiuses. Resilient and less porous, rosewood tends to absorb oils well, allowing it to preserve its rich, beautiful color.
'50s Rounded Neck Profile
No guitar neck profile is more distinguishable than the one employed on the Robot Les Paul Studio Limited ” the traditional '50s neck, which is the thicker, rounder profile, emulating the neck shapes found on the iconic 1958 and 1959 Les Paul Standards. Each neck is machined in Gibson's rough mill using wood shapers to make the initial cuts. Once the fingerboard is glued on, the neck is carefully shaped by hand. That means there are no two necks with exactly the same dimensions. True to its handcrafting, each neck will be slightly different, with a distinct and traditional feel.
Powerhead Locking Tuners
Gibson's Robot Les Paul Studio Limited is unique in many ways, but the "robot-like" Powerhead Tuners that grace the headstock are extraordinary. Pull out the Multi-Control Knob (MCK) and watch the Powerhead Tuners spring into action. It takes only a few seconds for the Powerhead Tuners to tune the Robot Les Paul Studio Limited to the desired tuning. Each tuning peg is equipped with a tiny but powerful servo motor that kicks into action once the system is activated. The Powerhead Tuners rely on the strings themselves to send the signals, eliminating any potential for interference. Made of lightweight metal with a satin nickel finish, the Powerhead Tuners weigh only 46.5 grams each. A standard Gotoh tuner weighs in at 49 grams. That means a set of Powerhead Tuners weigh a full 10 grams less than a set of Gotoh tuners, which is another indicator of the Robot Les Paul Studio Limited's true innovation.
The MCK is what is commonly referred to as a "push-pull" knob. When down in the normal position it behaves as a regular volume or tone pot. When the MCK is pulled out, the Robot Les Paul Studio Limited's radical self-tuning system is activated and ready for use. It immediately places the Robot Les Paul Studio Limited in standard tuning mode (A440). A quick turn of the MCK presents 6 factory presets, all of which can be customized. At any time, you can also restore the tunings to the factory presets and start all over again. The LED display on top of the MCK also lets you know when a string is out of tune, or when all strings are in tune, and even when the tuners are turning to get them in tune. It also guides the setting of accurate intonation. At the end of the tuning process, the blue lights on top of the MCK flash. Push the MCK back in and it's ready to go. Now the only thing you have to do is play.
Featuring a performance-safeguarding Neutrik jack, which secures the cord into the guitar, the Robot Les Paul Studio offers all the power, tone, and performance of a traditional Studio model, with the revolutionary Robot automatic tuning.
Neutrik jack
Neutrik has been making superior electronic interconnection products since 1975, making them the logical choice to supply the performance-safeguarding jack in Gibson's revolutionary Robot Les Paul Studio Limited. Like many Neutrik products, the jack in the Robot Les Paul Studio Limited is manufactured from strong, high-grade thermoplastics and housed in a rugged die-cast nickel shell. A retention spring inside the jack ensures optimum grip on any guitar cable, thus avoiding the chance of lost connection.
ChamberingChambering
There's something about playing a Gibson Les Paul with perfect tone, balance, and weight. One of the ways the expert craftsmen at Gibson USA achieve this equilibrium is by carving carefully mapped-out chambers in the solid mahogany backs of Les Pauls using a Computer Numeric Controlled (CNC) router before the maple top is glued on. The positioning of the routs was established after careful examination of the resonant characteristics of the Les Paul. Gibson approached this process with the awareness that every change to the formula would have repercussions on the instrument's sound. The results are comfortable, lightweight guitars that are acoustically louder, with increased sustain and resonance.
Mahogany Body and Maple Top
There isn't anything more fundamental to a Les Paul than a mahogany back with a maple top, as well as the process involved in selecting the right wood and the formula to dry it out. First, every piece of wood is personally inspected and qualified by Gibson's team of skilled wood experts before it enters the Gibson factories. Once inside the Gibson factories ” where humidity is maintained at 45 percent, and the temperature at 70 degrees ” all woods are dried to a level of "equilibrium" by ensuring the moisture content does not change during the manufacturing process. This guarantees tight fitting joints and no expansion, and helps control the shrinkage and warping of the woods, in addition to helping reduce the weight. It also helps with improving the wood's machinability and finished properties, and adherence to glue. Consistent moisture content means that a Gibson guitar will respond evenly to temperature and humidity changes long after it leaves the factory.
Nitrocellulose Finishes
Applying this nitro finish to any Gibson guitar ” including the Robot Les Paul Studio Limited ” is one of the most labor-intensive elements of the guitar-making process. A properly applied nitro finish requires extensive man hours, several evenly applied coats, and an exorbitant amount of drying time. But this fact has never swayed Gibson into changing this time-tested method that has been employed ever since the first Gibson guitar was swathed with lacquer back in 1894. Why? For starters, a nitro finish dries to a much thinner coat than a polyurethane finish, which means there is less interference with the natural vibration of the instrument, allowing for a purer tone. A nitro finish is also a softer finish, which makes it easily repairable. You can touch up a scratch or ding on a nitro finish, but you can't do the same on a poly finish. In addition, a nitro finish is very porous in nature, and actually gets thinner over time. It does not seal wood in an airtight shell ” as a poly finish does ” and allows the wood to breathe and age properly.
Tune-control Bridge and Data Transmitting Tailpiece
The revolutionary Robot Les Paul Studio Limited sports a unique, highly specialized Tune Control Bridge, which acts as one of the main components of the self-tuning robotic system. The Tune-Control Bridge is a modified Tune-o-matic that measures the individual tuning of each string via special saddles. The signal from each string is then transmitted to the control CPU in the control panel, which then transfers the signal to the Neck CPU and the Powerhead Locking Tuners, which, in turn, tune the strings. At first glance, the tailpiece on Gibson's groundbreaking Robot Les Paul Studio Limited looks like a normal tailpiece. But look a little closer and you'll see that it's far from ordinary. Gibson's Data Transmitting Tailpiece is a hub of activity. First, each string is separated by ceramic insulators that isolate each individual string signal and avoids confusion as to which string is being processed and tuned. There are also special isolating inserts that keep the ball ends commonly found on electric guitar strings from making contact and disrupting signal flow. Underneath the tailpiece is a tiny circuit board that processes each individual signal to the ribbon cable, which is then transmitted to the on-board CPUs. Both pieces work with each other to help balance all the information being transmitted between the various points, and makes sure every string is in tune.
The mid to late 1960s saw the emergence of a very different type of music coming from the clubs of England. The new genre's players were demanding more powerful amplifiers with increased volume outputs to satisfy their sonic explorations. This lead to a call for a more versatile pickup to split coils through a push/pull knob, and prevent the microphonic feedback that occurs when the volume is turned up to maximum levels. Gibson answered this call with the 490T and 490R pickups ("T" for treble, and "R" for rhythm), both with the traditional characteristics of the original "Patent Applied For" pickups, but with two key modifications. First, a four-conductor wiring scheme allows the 490s to be connected to any push/pull knob, which lets players split the coils and increase versatility. Gibson also introduced wax potting, which does away with any air space inside the pickup ” thus lessening the chances of microphonic feedback. The result is a humbucker with the tonal characteristics of an original PAF, with a slight increase in upper mid-range response. The Gibson 498T bridge pickup is the 490's ideal complement. Taking the 490 one step further, the 498 swaps the Alnico II magnet to an Alnico V, this making it slightly hotter with emphasis on mid-ranges and highs. The pole pieces on the 498T are also aligned a little further apart to accommodate the spacing of the strings at the bridge, which is different than the spacing of the strings at the neck. As with all Gibson pickups, every part is precisely manufactured at Gibson USA in Nashville, Tennessee.
Fret Wire
The fret wire on the revolutionary Robot SG Special Limited is a combination nickel and silver alloy (approximately 80 percent nickel and 20 percent silver) specifically designed for long life and superior wear. Gibson's traditional "medium-jumbo" fret wire is first shaped by hand, then cut to an exact 12" radius. After hand pressing it into the fingerboard, a machine press finished the job to eliminate the gap between the bottom of the fret wire and the fingerboard.
22-Fret Rosewood Fingerboard
Rosewood has always graced the fingerboards of the world's finest stringed instruments. The fingerboard on Gibson's Robot Les Paul Studio Limited is constructed from the highest grade Rosewood on the planet. It's personally inspected and qualified by Gibson's team of skilled wood experts before it enters the Gibson factories to be fitted onto the necks of the Robot Les Paul Studio Limited guitars. The resilience of this dense and durable wood makes the fingerboard extremely balanced and stable, and gives each chord and note clarity and bite. The 12" radius of the fingerboard provides smooth note-bending capabilities and eliminates "dead" or "choked out" notes, which can occur on fingerboards with lesser radiuses. Resilient and less porous, rosewood tends to absorb oils well, allowing it to preserve its rich, beautiful color.
'50s Rounded Neck Profile
No guitar neck profile is more distinguishable than the one employed on the Robot Les Paul Studio Limited ” the traditional '50s neck, which is the thicker, rounder profile, emulating the neck shapes found on the iconic 1958 and 1959 Les Paul Standards. Each neck is machined in Gibson's rough mill using wood shapers to make the initial cuts. Once the fingerboard is glued on, the neck is carefully shaped by hand. That means there are no two necks with exactly the same dimensions. True to its handcrafting, each neck will be slightly different, with a distinct and traditional feel.
Powerhead Locking Tuners
Gibson's Robot Les Paul Studio Limited is unique in many ways, but the "robot-like" Powerhead Tuners that grace the headstock are extraordinary. Pull out the Multi-Control Knob (MCK) and watch the Powerhead Tuners spring into action. It takes only a few seconds for the Powerhead Tuners to tune the Robot Les Paul Studio Limited to the desired tuning. Each tuning peg is equipped with a tiny but powerful servo motor that kicks into action once the system is activated. The Powerhead Tuners rely on the strings themselves to send the signals, eliminating any potential for interference. Made of lightweight metal with a satin nickel finish, the Powerhead Tuners weigh only 46.5 grams each. A standard Gotoh tuner weighs in at 49 grams. That means a set of Powerhead Tuners weigh a full 10 grams less than a set of Gotoh tuners, which is another indicator of the Robot Les Paul Studio Limited's true innovation.
Features
- Body Wood: Mahogany
- Top wood: Maple
- Scale Length: 24-3/4"
- Neck Joint: Set-in
- Neck Wood: Mahogany
- Fretboard: Rosewood
- Neck Shape: C-Shape
- Frets: 22 Medium-Jumbo
- Nut Width: 1.695"
- Fretboard Radius: 12
- Bridge: Tune-O-Matic
- Pickup Bridge: Gibson 498T Humbucker
- Pickup Neck: Gibson 490R Humbucker
- Controls: Volume/ Volume/Tone/Tone
- Tuners: Powerhead Locking
- Hardware color: Chrome
- Pickup selector: 3-way switch
- Finish: Nitrocellulose
- Includes case